Dustless Blasting or Sandblasting
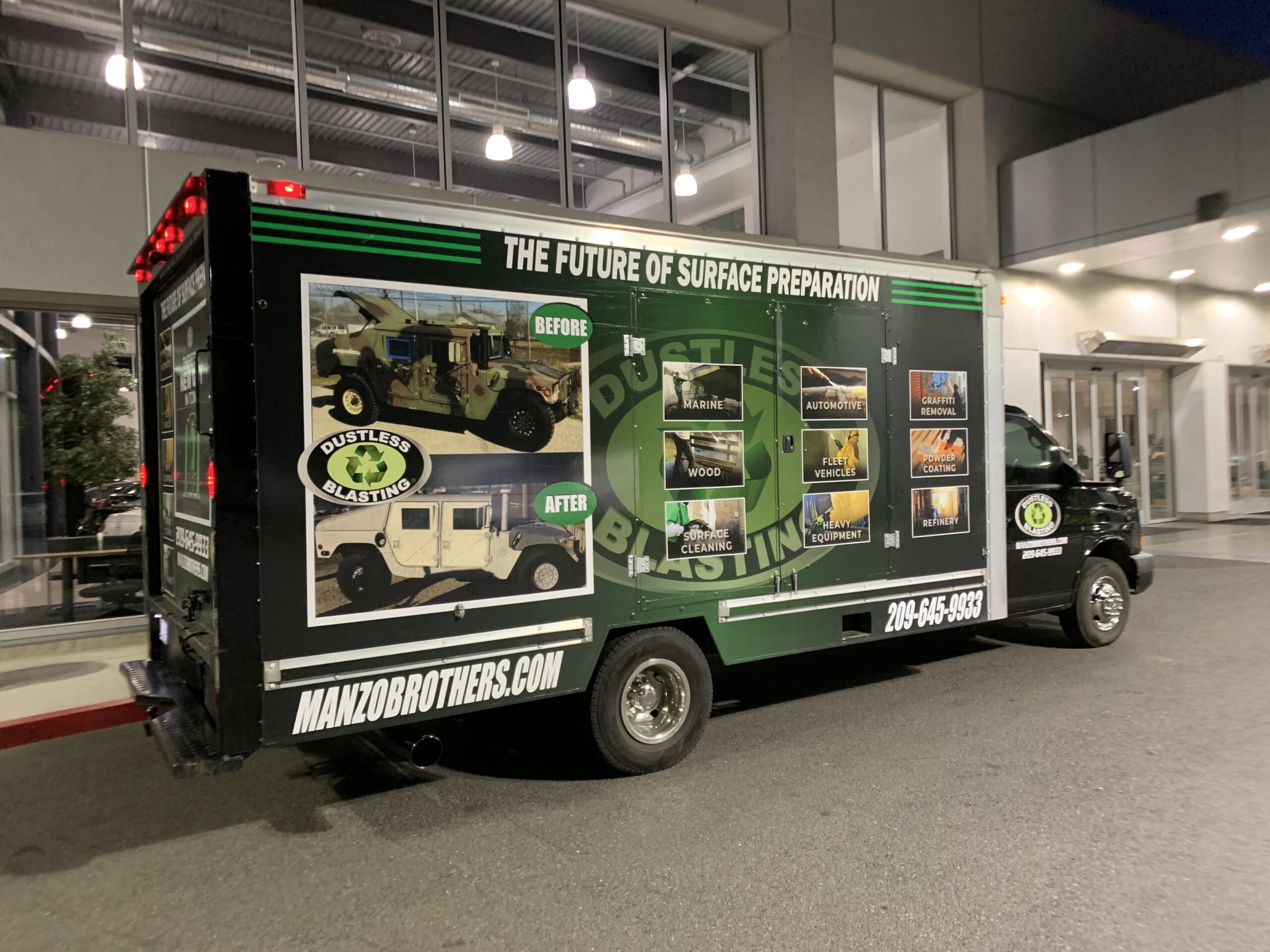
Dustless blasting and sandblasting are both abrasive blasting methods used for surface preparation, cleaning, and material removal. However, the key difference lies in the introduction of water in dustless blasting. Here’s a breakdown of each:
Sandblasting (Dry Abrasive Blasting):
Process: Involves propelling abrasive media (like sand, steel grit, glass beads, etc.) at a high velocity using compressed air to impact the surface.
Dust: Generates a significant amount of dust, consisting of the abrasive material and the removed coating or contaminant.
Applications: Effective for removing rust, old paint, and other tough coatings from various surfaces like metal, wood, and concrete. It can also be used to roughen surfaces for better adhesion of coatings or to create etched designs.
Considerations:
Dust Control: Requires proper containment and safety measures to protect the operator and the surrounding environment from airborne particles.
Heat Generation: Friction from the dry abrasive can generate heat, potentially warping thin metals.
Surface Damage: Can be too aggressive for delicate surfaces like thin aluminum or glass.
Cleanup: Can be messy due to the dispersed abrasive material.
Cost: Generally less expensive than dustless blasting in terms of initial equipment.
Dustless Blasting (Wet Abrasive Blasting, Vapor Blasting, Slurry Blasting):
Process: Similar to sandblasting, but water is mixed with the abrasive media at the nozzle.
Dust: The water encapsulates the abrasive particles and the removed material, significantly reducing or eliminating airborne dust.
Applications: Versatile and can be used on a wider range of materials, including those sensitive to heat or warping (like thin metals and wood). Effective for removing paint, rust, grease, and other contaminants. It can also be used for cleaning delicate surfaces and even graffiti removal.
Considerations:
Dust Suppression: The primary advantage is the near elimination of dust, making it safer for the operator and the environment, and often negating the need for extensive containment.
Reduced Heat: The water helps to dissipate heat, minimizing the risk of warping.
Gentler on Surfaces: The cushioning effect of the water allows for use on more delicate materials.
Cleanup: While there’s no dust cloud, you’ll have a wet slurry of abrasive and removed material to manage.
Rust Inhibitors: Often, rust inhibitors are added to the water to prevent flash rusting on metal surfaces after blasting.
Cost: Equipment can be more expensive than traditional sandblasting setups.
Which to Choose?
The best method depends on the specific project and your priorities:
Choose Sandblasting if:
The project involves robust materials that are not susceptible to warping.
Effective dust containment measures can be implemented.
Cost is a primary concern.
The application requires a very aggressive abrasive action.
Choose Dustless Blasting if:
Dust control is a major concern due to environmental regulations or nearby personnel/property.
The materials being blasted are delicate or prone to warping.
A gentler but still effective cleaning method is needed.
The added benefit of rust inhibition is desired for metal projects.
In summary, dustless blasting offers a cleaner, often safer, and more versatile alternative to traditional sandblasting, albeit potentially at a higher initial cost.